Chemisches Recycling von Kunststoffen – Chancen und Herausforderungen
Kunststoffe sind weltweit ein wichtiger Wirtschaftsfaktor und als universelle Komponente für Produkte und Einsatzzwecke aller Art allgegenwärtig. Umso dringender sind daher die damit verbundene Umwelt-, Klima- und Rohstofffragen zu klären. Eine Lösung heißt „Recycling“. Denn Fakt ist: Immer noch landen viele Kunststoffabfälle in der Müllverbrennung, auf Deponien und unsachgemäß in der Natur. Da das etablierte mechanische Recycling technisch an seine Grenzen stößt, richten sich die Hoffnungen zur Erhöhung der Recyclingquoten auf das chemische Recycling von Kunststoffabfällen. Dieser Überblick zeigt, dass es Chancen bietet, aber auch noch einige anspruchsvolle Herausforderungen bis zu einer großtechnischen Lösung zu überwinden sind.
Kunststoffe sind aus unserem täglichen Leben nicht mehr wegzudenken, weil sie in vielen Anwendungsbereichen nützlich und kostengünstig einsetzbar sind. So ist die hygienische Verpackung von Lebensmitteln auf bestimmte qualitativ hochwertige Kunststoffe angewiesen. Entsprechend wird dieses Material überwiegend für Verpackungen verwendet (44 Prozent), aber auch in Bereichen wie dem Baugewerbe (18 Prozent), der Automobilindustrie (8 Prozent), der Elektro- und Elektronikindustrie (7 Prozent) sowie Haushalt, Freizeit und Sport (7 Prozent). Die Herstellung von Kunststoff ist ebenso ein großer Wirtschaftsfaktor mit mehr als 52.000 Unternehmen und über 1,5 Millionen Beschäftigten in der EU.
Kunststoffe spielen dabei eine zunehmend wichtige Rolle für viele technische Anwendungen. Die Leistungen moderner Windkraftanlagen wären ohne Kunststoffe nicht erreichbar, betriebssichere Isolierung aktuell nicht wirtschaftlich darstellbar Diese Beispiele zeigen: Kunststoffe sind wichtiges Material für die Transformation und werden daher langfristig gebraucht. Dafür müssen sie jedoch selbst CO2-neutral hergestellt werden und die negativen Folgen der Nutzung insbesondere durch Plastikmüll gelöst werden. Derzeit werden rund 10 Prozent der europäischen Produktion aus recycelten Kunststoffabfällen hergestellt.
Noch große Herausforderungen für Klima- und Umweltschutz
Nur wenige Länder wie die Niederlande, Norwegen, Spanien und Deutschland erreichen Kunststoffrecyclingraten von mehr als 40 Prozent. Der Großteil der weltweit erzeugten festen Kunststoffabfälle (d.h. über 70 Prozent) wird weiterhin auf Deponien und/oder unsachgemäß in der Umwelt entsorgt, insbesondere wenn es keine funktionierenden Sammlungs- und Verwertungssysteme gibt.
Durch ihre lange Haltbarkeit verläuft der Abbauprozess von deponierten und weggeworfenen Kunststoffen je nach Umgebungsbedingungen und Art des Kunststoffs nur sehr langsam und kann viele Jahre dauern. Das macht sie zu einem Umweltproblem. So können sich Kunststoffe als Mikroplastik in Böden, Gewässern und Meeren anreichern und darüber auch in unsere Nahrung gelangen. Welche gesundheitlichen Folgen das haben könnte, ist noch Gegenstand von Untersuchungen. Für die Herstellung von Kunststoffen sind zudem heute noch Einsatzstoffe und Energieträger erforderlich, die weit überwiegend aus fossilen Rohstoffen wie Erdöl und Erdgas stammen, wodurch CO2 freigesetzt wird. Auch diese Moleküle müssen zukünftig aus nachhaltigen Quellen kommen.
Kreislaufwirtschaft mit Recycling ist wichtiger Teil der Problemlösung
In einer Kreislaufwirtschaft werden Produkte und Materialien möglichst lange geteilt, geleast, wiederverwendet, repariert und aufgearbeitet bis sie schließlich recycelt werden. Das Ziel ist, Abfälle auf ein Minimum zu reduzieren sowie Produkte und Rohstoffe CO2-neutral im Wirtschaftskreislauf zu nutzen.
Vorteile der Substitution zunehmend knapper fossiler und natürlicher Rohstoffe durch Kreislaufwirtschaft mit Recycling:
- Rohstoffabhängigkeit reduzieren:
Ressourcen werden knapp. Eine Reihe wichtiger Rohstoffe ist nur begrenzt verfügbar und da die Weltbevölkerung wächst, steigt auch die Nachfrage nach Rohstoffen. - Klimaschutz:
Ein weiterer Vorteil der Kreislaufwirtschaft ist eine Reduzierung der gesamten jährlichen Treibhausgasemissionen. - Umweltschutz:
Schutz von Landschaften und Lebensräumen und trägt dazu bei, den Verlust der biologischen Vielfalt zu begrenzen. - Wertschöpfung und Arbeitsplätze:
Der Übergang zu einer stärker kreislauforientierten Wirtschaft könnte die Wettbewerbsfähigkeit steigern, Innovationen anregen, das Wirtschaftswachstum ankurbeln und Arbeitsplätze schaffen (700.000 Arbeitsplätze allein in der EU bis 2030).Die Neugestaltung von Materialien und Produkten für die Kreislaufnutzung würde auch die Innovation in verschiedenen Wirtschaftssektoren fördern.
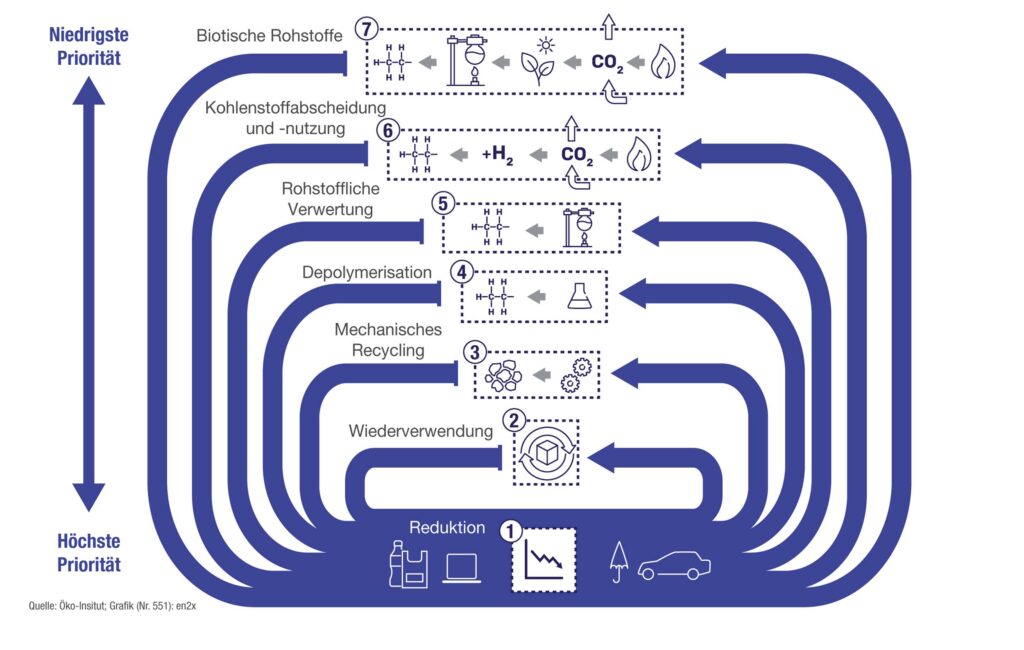
Angesichts des aktuell geringen Anteils recycelter Kunststoffe ist ein Übergang zu einer stärker kreislauforientierten Wirtschaft ein wichtiger Weg. Dies könnte dabei helfen, Ressourcen zu schonen und Abhängigkeiten zu reduzieren, Treibhausgasemissionen zu mindern und die Umwelt zu schützen. Innovationen in der Kreislaufwirtschaft könnten das Wirtschaftswachstum fördern und zu neuen Arbeitsplätzen führen und damit die Wettbewerbsfähigkeit steigern.
Das mechanische Recycling stößt an seine Grenzen
Die EU versucht, Kunststoffabfälle durch sogenanntes „Ökodesign“ zu verringern, etwa durch den Ersatz von Einwegkunststoffen durch alternative oder mehrfach verwendbare Materialien bis hin zur Steigerung der Produktion von Rezyklaten durch mechanisches Recycling. Der Begriff mechanisches Recycling beschreibt stark vereinfacht ausgedrückt Verfahren, bei dem Kunststoffe thermisch geschmolzen und in neue Formen gebracht werden. Das mechanische Recycling (auch werkstoffliches Recycling genannt) von Kunststoffen ist heute bereits weit verbreitet und damit der wichtigste Baustein für die Wiederverwendung von Kunststoffabfällen als wertvollen Kohlenstoffrohstoff.
Hintergrund: Bei Kunststoffen handelt es sich um lange Molekülketten. Die einzelnen „Kettenglieder“ heißen Monomere. Zusammen bilden sie lange Ketten, die sogenannten Polymere. Viele Kunststoffe tragen daher das Präfix „Poly-“ im Namen. Beim mechanischen Recycling wird die Polymerstruktur nicht wesentlich verändert, sodass der Kunststoff als Werkstoff erhalten bleibt. Der Schwerpunkt des Recyclings liegt auf sortenreinen, größeren werthaltigen Fraktionen von Kunststoffen wie PET (Polyethylenterephthalat), PP (Polypropylen) oder PE (Polyethylen), die zum Bespiel durch Pfandsysteme für PET-Flaschen in geschlossenen Kreisläufen geführt und daher mehrmals recycelt werden können. Allerdings ist dies nur ein kleiner Teil aller Kunststoffabfälle. Viele insbesondere gemischte Kunststoffe würden beim mechanischen Recycling an Qualität und Haltbarkeit verlieren. Die verschiedenen Polymerketten würden sich verbinden und es entsteht ein Mischkunststoff, der in vielen Anwendungen insbesondere mit Lebensmittelkontakt ungeeignet ist. Das führt dazu, dass in der EU mehr als die Hälfte der Post-Consumer-Kunststoffabfälle nicht recycelt werden, sondern in der Abfallverbrennung landen oder auf Deponien gelagert werden.
Aufgrund dieser Einschränkungen des mechanischen Recyclings ist es mit diesen Verfahren allein absehbar nicht möglich, die europäischen Recyclingziele der Abfallrahmenrichtlinie und des europäischen Verpackungsgesetzes zu erreichen.
In Fachkreisen wird daher das chemische Kunststoffrecycling ergänzend zum mechanischen Recycling als eine Option zur Erreichung der Ziele angesehen. Es eröffnet die Perspektive, dass chemisches Recycling einerseits in der Lage ist, technisch aufwändiger zu verarbeitende Kunststoffabfälle umzusetzen und dadurch das Spektrum der recycelbaren Kunststoffe und damit die Recyclingquoten zu erhöhen. Andererseits könnte es auch dazu beitragen, Recyclingmaterial in kontaktsensitiven Anwendungen einzubringen.
Chemisches Recycling – unterschiedliche Verfahren
Während beim mechanischen Recycling von Kunststoffabfällen die chemische Grundstruktur der Polymere erhalten bleibt, wird sie beim chemischen Recycling (auch rohstoffliches Recycling genannt) aufgebrochen durch den Einsatz von Lösungsmitteln, Reaktionsmitteln, Temperatur und/oder Druck. So entstehen wertvolle chemische Bausteine, das heißt kleinere Moleküle (Monomere), Polymere, Grundchemikalien und/oder Zwischenprodukte. Die gewonnenen chemischen Bausteine dienen für die chemische Industrie als Ausgangsmaterial zur Herstellung neuer Produkte. Das können neue Kunststoffe sein, doch auch andere Chemikalien und theoretisch auch Kraftstoffe lassen sich daraus herstellen.
Je nach dem Prinzip oder Verfahren der Zersetzung von Kunststoffen, kann beim chemischen Recycling unterschieden werden zwischen
- Pyrolyse (Thermochemisches Recycling),
- katalytischem Cracken ((Thermokatalytisches Recycling)),
- Hydrocracking,
- Solvolyse (Chemischer Depolymerisation),
- Hydrolyse und Vergasung (Gasifizierung).
Pyrolyse (Thermochemisches Recycling)
Bei der Pyrolyse werden aufbereitete Kunststoffabfälle, die langkettige Polymermoleküle enthalten, unter Ausschluss von Sauerstoff erhitzt, so dass der Kunststoff zu kürzeren Kohlenwasserstoffmolekülen zerfällt. Der Prozess benötigt Temperaturen von etwa 300 bis 600°C und mehr. Die Verweilzeit der Abfälle unter den Temperaturen verkürzt sich mit steigenden Temperaturen und beträgt von vielen Stunden bis zu wenigen Sekunden, bis die Abfälle umgesetzt sind. Das aus der Pyrolyse resultierende Produktspektrum ist relativ breit und hängt vom Ausgangsstoff, den Prozessbedingungen, dem Reaktortyp und dem Verfahrensdesign ab. Zu den Hauptprodukten zählt sogenanntes Pyrolyseöl, das durch Destillation und Veredelung zu marktfähigen Produkten wird. Es kann wie konventionelles Rohöl beispielsweise in einer Raffinerie wieder zu Monomeren zur Herstellung von Kunststoffen verarbeitet werden. Diese Kunststoffe sind dann chemisch nicht mehr von den heutigen Primärkunststoffen zu unterscheiden. Auch die Herstellung von Grundchemikalien für die Petrochemie ist möglich. Neben dem Pyrolyseöl fallen als Nebenprodukte auch feste und gasförmige Rückstände an. Diese können energetisch oder stofflich genutzt werden.
Katalytisches Cracken (Thermokatalytisches Recycling)
Das thermokatalytische Recycling, auch katalytisches Cracken genannt, ist eine Pyrolyse mit einem katalytischen Material. Der Katalysator beeinflusst die Zersetzungsreaktion mit dem Ziel, die Prozesstemperaturen zu verringern und damit Energie zu sparen, oder die selektive oder generelle Ausbeute bestimmter Produkte zu erhöhen. Der übliche Temperaturbereich thermokatalytischer Vorgänge reicht von 300 bis 900°C, abhängig vom verwendeten Reaktortyp, dem Druck und den erwünschten Ergebnissen.
Die Verwendung von katalytischen Materialien macht den Pyrolyseprozess anfälliger für Störungen und erfordert erhöhten technischen Aufwand. Der Einsatzstoff muss eine höhere Qualität besitzen, denn durch bestimmte Kunststoffsorten können Verunreinigungen wie Stickstoff oder Schwefel in den Prozess gelangen, die als Katalysatorgifte den Prozess beeinträchtigen würden. Auch andere Störstoffe wie sich bildender Koks können die Wirkung des Katalysators durch Ablagerungen oder chemische Reaktionen schwächen, so dass der Katalysator regeneriert werden muss. Das trifft auf viele Verfahren in der (petro)chemischen Industrie zu, doch in der Regel sind mit zunehmender technischer Erfahrung derartige Probleme beherrschbar.
Hydrocracking
Das Hydrocracking ähnelt der thermochemischen Pyrolyse und dem katalytischen Cracking mit dem Unterschied, dass Wasserstoff hinzugefügt wird. Unter Klimagesichtspunkten wird dieser Wasserstoff nachhaltig erzeugt werden müssen (grüner Wasserstoff). Oft wird in den Prozess auch ein Katalysator eingebunden. Der Wasserstoff kann dann unter anderem entstehende Doppelbindungen sättigen und anderweitig die chemische Ölqualität verbessern. Die Produkte ähneln dann fossilem Erdöl stärker, sodass bekannt hohe Produktqualitäten und stabilere Verbindungen erreicht werden können. Dieser Prozess wird bereits in Raffinerien für die Rohöldestillation eingesetzt und eignet sich auch für das Kunststoffrecycling. Möglich ist auch eine gemeinsame Verarbeitung von Feedstocks aus dem chemischen Recycling und anderen fossilen oder sonstigen erneuerbaren Quellen. Durch die Verdünnung ist es möglich, die Effekte von Katalysatorengiften und Ablagerungen zu begrenzen.
Für die Zersetzungsreaktionen sind relativ geringe Temperaturen von etwa 400°C und eine Verweildauer von bis zu 60 Minuten üblich.
Solvolyse (Chemische Depolymerisation)
Die Solvolyse (auch Chemolyse oder chemische Depolymerisation genannt) ist ein alternatives Verfahren zur Pyrolyse. Für die Zersetzung werden unterschiedliche Lösungsmittel (chemische Reagenzien) eingesetzt, die zu verschiedenen Recyclingprodukten führen. Ausgehend von den Reagenzien gibt es daher als hauptsächliche solvolytische Verfahren die Glykolyse, Methanolyse, Hydrolyse sowie die Ammonolyse und Aminolyse. Die Solvolyse findet im Temperaturbereich von 150 bis 300°C statt und kann durch den Einsatz von Katalysatoren beschleunigt werden. Da solvolytische Verfahren nur für Polykondensationskunststoffe wie Polyester und Polyamide geeignet sind, die lediglich einen kleinen Teil des Aufkommens an Kunststoffabfällen darstellen, können sie nur einen kleinen Beitrag zur Erhöhung der Recyclingquoten leisten.
Gasifizierung
Die Gasifizierung (Vergasung) ist ein thermo-chemischer Zersetzungsprozess, bei dem ein kohlenstoffhaltiges Material zusammen mit Sauerstoff, Luft, Wasserdampf oder Mischungen daraus oxidiert wird (partielle Oxidation). Dafür sind hohe Temperaturen von 700 bis 1.600°C und Drücke zwischen 20 und 80 bar erforderlich. Als Produkt dieses Prozesses entsteht ein idealerweise möglichst reines Gas (Synthesegas), das hauptsächlich aus Kohlenstoffmonoxid (CO) und Wasserstoff (H2) besteht. Allerdings entstehen im Prozess auch feste Ruckstände wie Asche, Schlacke, Flugasche und Ruß. Die Verwendung von Synthesegas ist in der chemischen Industrie weit verbreitet und dient in etablierten Prozessen etwa zur Herstellung chemischer Grundstoffe. Es ist auch möglich, aus dem Synthesegas ein Fisch-Tropsch-Syncrude herzustellen. Dieses kann dann als direkter Ersatz für fossiles Erdöl dienen.
Herausforderungen des chemischen Recyclings
In der Regel sind chemische Recyclingverfahren weniger sensitiv gegenüber Additiven, Schadstoffen und Verunreinigungen in Kunststoffabfällen als mechanische Recyclingverfahren. Das gilt vor allem für die thermische Pyrolyse und die Gasifizierung. Im Gegensatz zum mechanischen Recycling können die im chemischen Recycling gewonnenen Bausteine teilweise auch zu lebensmitteltauglichen oder berührungsempfindlichen Kunststoffen verarbeitet werden.
Dennoch sind auch im chemischen Recycling die vorbereitenden Schritte Sortierung, Trennung, Reinigung, Waschung, Trocknung und Zerkleinerung für die Aufbereitung zum Recycling erforderlich. Die eingesetzten Kunststoffabfälle wirken sich bei allen Verfahren stark auf die Produktqualität aus. Die flüssigen Produkte aus dem Kunststoffrecycling müssen bestimmte physikalisch-chemische Spezifikationen erfüllen, damit sie in weiterführenden Verarbeitungsanlagen, etwa zur Herstellung neuer Kunststoffe eingesetzt werden können. Die Verarbeitung sollte daher verdünnt zusammen mit anderen Komponenten im Co-Processing erfolgen. Dennoch ist es erforderlich die chemischen Verfahren so weiterzuentwickeln, dass Sortierreste chemisch verwertbar ohne zusätzlichen Aufwand verwertbar sind. Um Konkurrenzsituationen zu vermeiden, muss die Sortierung und Trennung von Kunststoffabfällen weiterhin in eine Veredelungskette integriert werden, in der auch Nebenprodukte und die Reststoffe umweltverträglich behandelt beziehungsweise thermisch verwertet werden.
Auf die Wirtschaftlichkeit des chemischen Recyclings wirken sich überwiegend regulatorische Rahmenbedingungen aus. Ohne praktikable Methoden zum Co-Processing von Pyrolyseölen mit anderen Feedstocks wird keine Anlage gebaut werden und Lösungen für die Umweltprobleme durch Plastikmüll rücken in weite Ferne.
Noch keine aussagekräftige Ökobilanzierung möglich
Untersuchungen haben gezeigt, dass das chemische Recycling im Vergleich zur energetischen Verwertung von Kunststoffabfällen in Müllverbrennungsanlagen niedrigere Treibhausgasemissionen und einen geringeren Verbrauch fossiler Ressourcen verursacht. Allerdings gibt es noch nicht genügend Daten zu chemischen Recyclingprozessen in der Praxis, auf deren Grundlage aussagekräftige ökologische Bewertungen möglich wären. Eine aussagekräftige und vergleichbare Datengrundlage für Massen-, Energie- und Kohlenstoffbilanzen und somit die Grundlage für belastbare Ökobilanzierungen kann erst aus dem Langzeitbetrieb entsprechender Anlagen mit einem hohen technologischen Reifegrad gebildet werden.
Erste Projekt in einem Zukunftsmarkt für chemisches Recycling
Anfang 2024 gab es nach Angaben von Ecoprog, einem Beratungsunternehmen in der Umwelt- und Energietechnik, weltweit erst gut 40 Anlagen zum chemischen Recycling. Darunter befinden sich nur sehr wenige großtechnische Anlagen.
Auch Unternehmen der Mineralölwirtschaft sind im chemischen Recycling aktiv, wie zum Beispiel OMV und Neste:
- OMV betreibt in seiner Raffinerie im österreichischen Schwechat eine Anlage im selbst entwickelten ReOil®-Verfahren, bei dem es sich um einen Pyrolyseprozess mit dem Ziel der Herstellung synthetischen Rohöls handelt, das von der Borealis in Sichtweite der Anlage direkt neuen Kunststoffen weiterverarbeitet werden kann.
- Neste entwickelt aktuell in seiner Raffinerie im finnischen Porvoo eine Technologie zur Pyrolyse von Kunststoffabfällen mit dem Ziel, das Rezyklat für die Herstellung neuer Kunststoffe zu nutzen. Die Entwicklungsaktivitäten finden innerhalb des EU-Forschungsprojekts „Pulse“ statt.
Gegenüber den Bestandsanlagen zählt Ecoprog mehr als 110 projektierte chemische Recyclinganlagen. Demnach sind 20 Anlagen zum chemischen Recycling auf der ganzen Welt im Bau, bis 2026 sollen insgesamt 50 Anlagen entstehen. Im Bestand und in der Projektierung befinden sich überwiegend Plastics-to-Plastics-Anlagen.
Ausblick
Das chemische Recycling bietet eine Perspektive, künftig gemischte Kunststoffabfälle und Verbundwerkstoffe zu verarbeiten, die aktuell nicht oder nur mit hohem Aufwand recycelt werden können, und so die Recyclingquoten zu erhöhen. Es gibt einen Markt für P2P-Rezyklate, der angesichts der zunehmenden Nachfrage von Konsumenten nach recycelten Kunststoffen und der zu erwartenden Anpassung rechtlicher Rahmenbedingungen künftig wachsen dürfte. Allerdings befinden sich die meisten chemischen Recyclingtechnologien noch in einem sehr frühen Entwicklungsstadium. Die meisten der bestehenden Anlagen sind noch Pilotanlagen, die weiterer Entwicklungsarbeit bedürfen, um anlagen- und prozesstechnische Herausforderungen zu lösen, die Technologien effizienter zu gestalten und sie auf größere Betriebseinheiten zu skalieren. Für den Hochlauf der Technologie werden verlässliche Rahmenbedingungen, besonders zur Mitverarbeitung von chemischen Rezyklaten benötigt.
AKTUELLE BEITRÄGE
Droht Raffinerien 2040 das Aus?
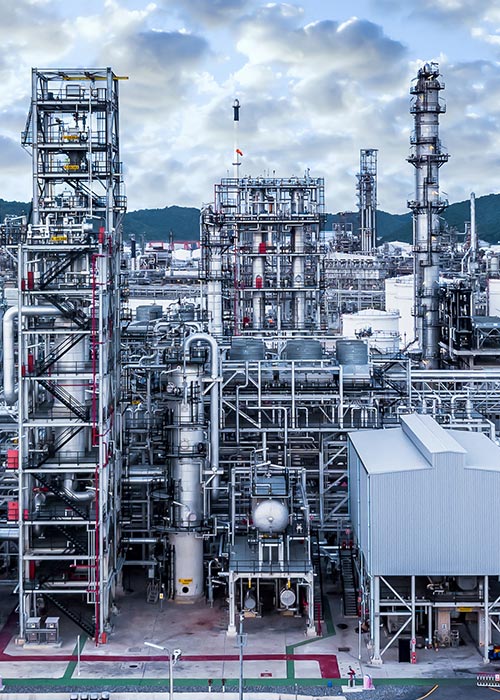